Understanding Conveyor Systems
Conveyor Systems are mechanical devices or assemblies that transport material with minimal effort. While there are many different kinds of conveyor systems, they usually consist of a frame that supports either rollers, wheels, or a belt, upon which materials move from one place to another. They may be powered by a motor, by gravity, or manually. These material handling systems come in many different varieties to suit the different products or materials that need to be transported.
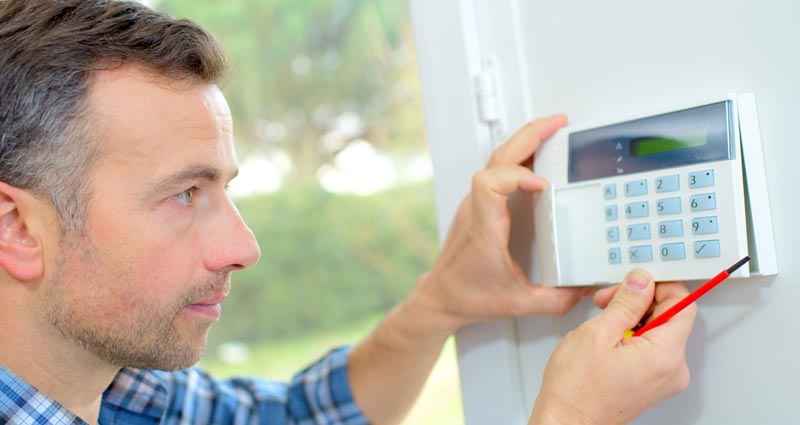
Belt Conveyor
Belt Conveyors are material handling systems that use continuous belts to convey products or material. The belt is extended in an endless loop between two end-pulleys. Usually, one or both ends have a roll underneath. The conveyor belting is supported by either a metal slider pan for light loads where no friction would be applied to the belt to cause drag or on rollers. Power is provided by motors that use either variable or constant speed reduction gears.
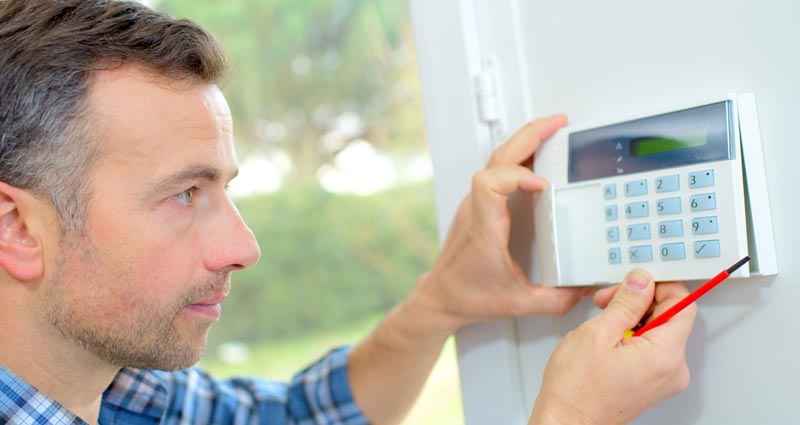
Roller Conveyor
Roller Conveyors use parallel rollers mounted in frames to convey product either by gravity or manually. Key specifications include the roller diameter and axle center dimensions. Roller conveyors are used primarily in material handling applications such as on loading docks, for baggage handling, or on assembly lines among many others. The rollers are not powered and use gravity, if inclined, to move the product, or manually if mounted horizontally. The conveyors can be straight or curved depending on the application and available floor space.
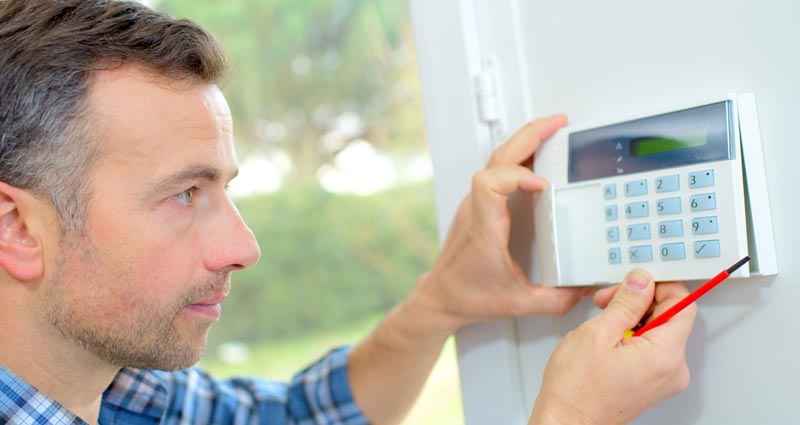
Powered Roller Conveyor
Powered Roller Conveyors use powered rollers mounted in frames to convey products. Key specifications include the drive type, roller diameter and material, and the axle center dimension. Powered roller conveyors are used primarily in material handling applications that require the powered conveyance of the product. Various drive types include belts, chains/sprockets, and motorized rollers. Some of the uses of powered roller conveyors are food handling, steelmaking and, packaging.
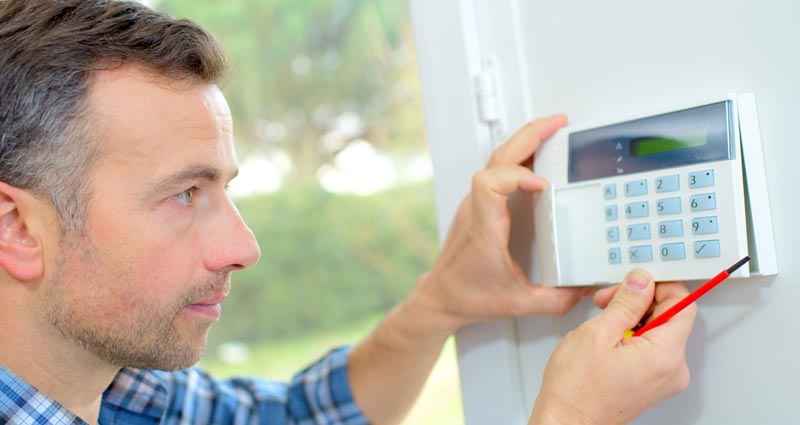
Slat Belt Conveyor/Apron Conveyor
Apron/Slat Conveyors use slats or plates made of steel, wood, or other materials typically mounted on roller chains to convey product. The slats are not interlocked or overlapping. Apron/slat conveyors are used primarily in material handling applications for moving large, heavy objects including crates, drums, or pallets in heavy-industry settings such as foundries and steel mills. The use of slats in heavy duty use cases prolongs the service life of the conveyor over other conveyor types that employ belts, which would wear out quicker under the exposure to heavy loads.
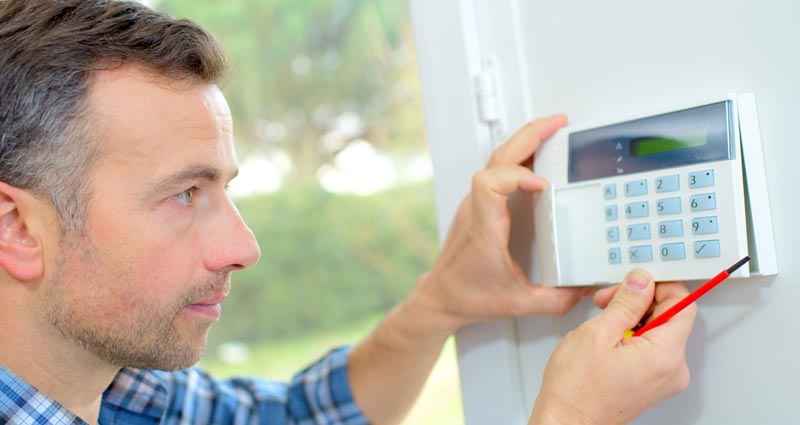
Chute Conveyor
Chute Conveyor is one of the least expensive methods of conveying material. It is the simplest example of gravity-operated conveyor. Chute conveyor is used to provide accumulation in shipping areas; a spiral chute can be used to convey items between floors with minimum amount of space required
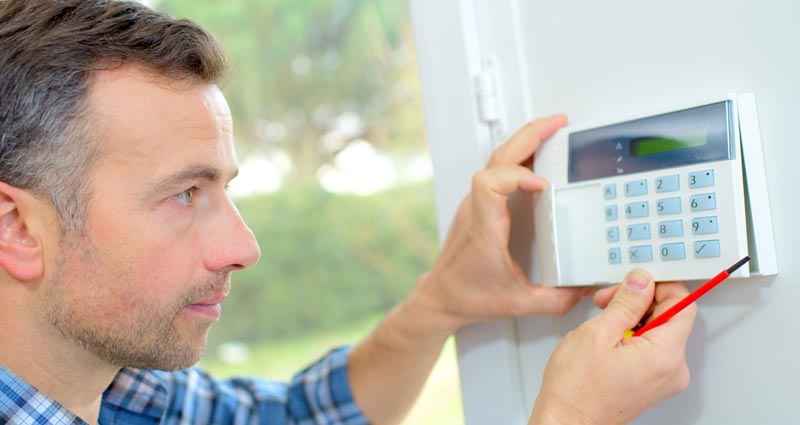
Overhead Conveyor
Overhead conveyors free up valuable floor space by moving conveying systems up above work areas. A continuous track is suspended either from overhead supports and pendants are placed on the track that can hold product to be conveyed. One of the most common types of conveyor, an overhead conveyor is generally used in a production facility to move parts from one location to another. They take advantage of the generally unused vertical space above the working area.
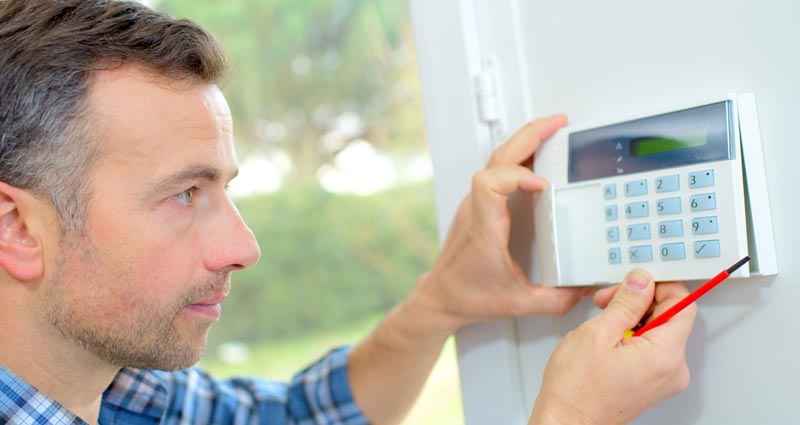
Vertical Conveyor
The most common applications of vertical conveyors are for reducing floor space, tying multiple floors together, vertical accumulation systems, pick-up and drop-off points for vehicles, and many many more specific use cases. They find applications in airports, automotive manufacturing, chemical processing, food packaging, recycling, warehouse distribution, and other industries.
Load Capacity per Unit Length.
Manufacturers will offer this attribute in cases where the conveyor will be built to a custom length to permit users to determine loading margins.
Maximum Load Capacity
Associated with Load Capacity per Unit Length, this value can be stated for fixed length, purpose-built conveyors. This can also be known as flow rate.
Conveyor Belt System Speed/Rated Speed
Belt conveyors are typically rated in terms of belt speed in ft/min. while powered roller conveyors described the linear velocity in similar units to a package, carton, etc. moving over the powered rollers. Rated speed applies to apron/slat conveyors and drag/chain/tow conveyors as well.
Throughput
Throughput measures the capacity of conveyors that handle powdered materials and similar bulk products. It is often given as a volume per unit time, for instance, as cubic feet per minute. This attribute applies to bucket, pneumatic/vacuum, screw, vibrating, and walking beam conveyors.
Frame Configuration
Frame configuration refers to the shape of the conveyor frame. Frames can be straight, curved, z-frames, or other shapes.
Drive Location
Drives can be located in different places on conveyor systems. A head or end drive is found on the discharge side of the conveyor and is the most common type. Center drives are not always at the actual center of the conveyor, but somewhere along its length, and are mounted underneath the system. They’re used for reversing the direction of a conveyor.